At Royal Welding Wires, we produce some of the best cutting electrodes on the market. We’ve got everything you need to be successful in your welding experience.
Electrodes are one of the most important and commonly used equipment in laboratory settings. In this article, we will discuss the different types of electrodes and what purpose they serve.
Additionally, we will provide tips on how to cut electrodes properly so that you don’t end up with defective or unusable materials.
Why do I need to know about cutting electrodes?
There are a few reasons why you might need to cut electrodes. For one, if the electrode is not fitting correctly or is damaged, you might need to cut it off so it can be replaced.
Additionally, electrodes can be cut if they’re too long or too short, which could lead to problems with the electrical current flowing through the electrode. In some cases, cutting an electrode can make it work better.
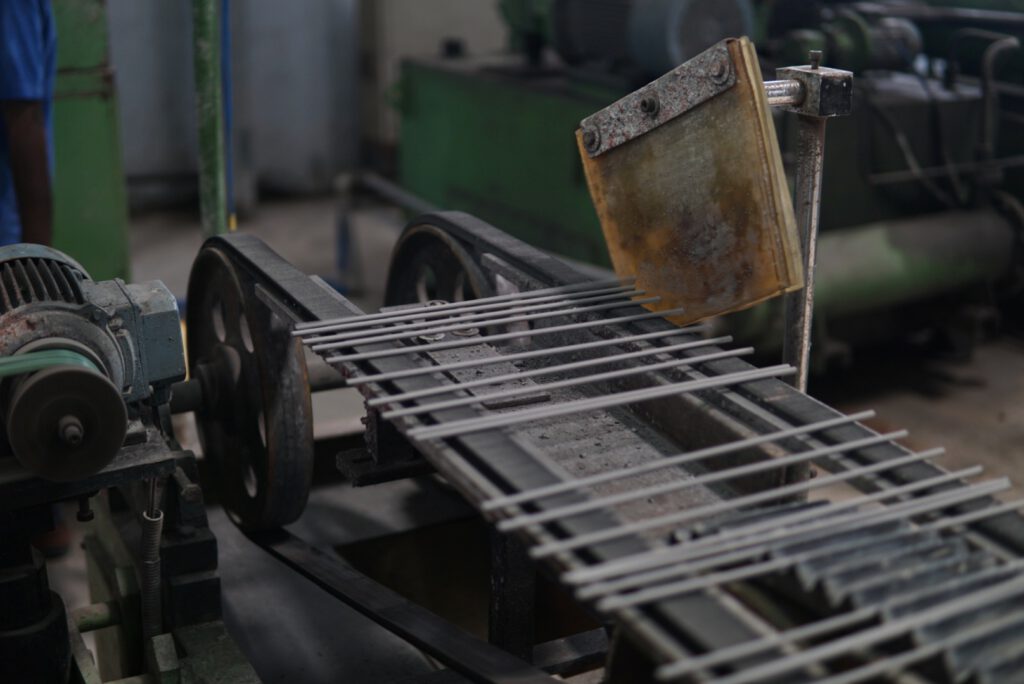
How do I use the cutting electrodes?
Electrodes create a well in a patient’s skull during neurosurgery. The electrodes are inserted into the patient’s brain through small incisions.
There are different types of cutting electrodes, but all have a single purpose: to make a well in the skull so that surgery can be performed.
There are three main types of cutting electrodes: rotary, bipolar, and multipolar. Each has its specific uses and requires different techniques for insertion and usage.
Rotary cutting electrodes are used most often for brain and spinal cord surgeries. These electrodes have a rotating wheel at their tip that cuts through the skull easily.
To use these electrodes, surgeons first insert them into the scalp using a drilling tool. Then they guide the electrode wheel around the patient’s head until it finds the spot they want to cut. After locating the target, they pull the wheel back slightly and use a surgical saw to make the hole.
Revolutionize your cutting game with our expert guide to cutting electrodes. Click now to discover the ultimate tips and tricks to boost your efficiency and save money. Don’t wait, take your cutting to the next level today.
What are the best materials to manufacture cutting electrodes from?
A few different types of materials can be used to make cutting electrodes. The most popular types of materials are metals, plastics, and ceramics. Each of these materials has unique properties, making it the best option for manufacturing cutting electrodes.
Metals are the most popular material for manufacturing cutting electrodes because they are strong and versatile.
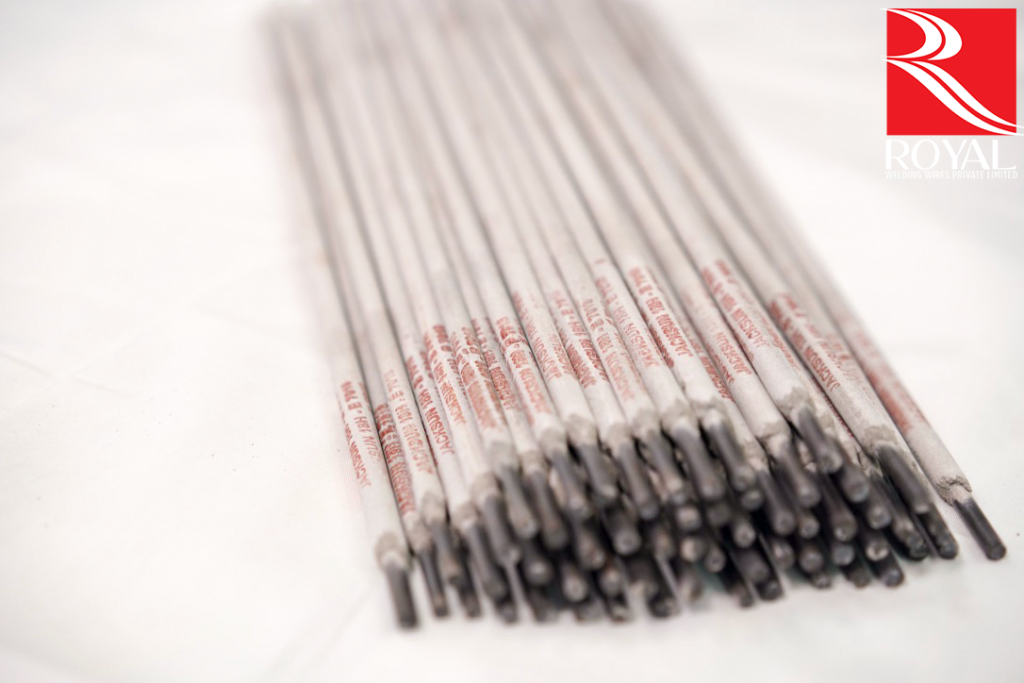
They can be easily shaped and have a wide range of electrical properties. Metal-cutting electrodes made from stainless steel are particularly popular because they are strong and durable.
However, metal cutting electrodes made from other metals also have several advantages. For example, gold-plated metal cutting electrodes are often used in electrochemistry because they have a high conductivity.
What are the different types of cutting electrodes?
A few different types of electrodes can be used in electroplating. The most common type is the copper electrode, which deposits metals onto other substrates.
Other types of electrodes include silver and gold electrodes, which are used for plating with those metals, and nickel-cadmium and nickel-metal-hydride electrodes, which are used for electroplating with cadmium and nickel.
How can I get the best quality and performance from my cutting electrodes?
When it comes to cutting electrodes, you want to ensure that you get the best quality and performance for your money. Here are a few tips to help you get the most out of your electrodes:
- Look for electrode brands tested and approved by the safety institute SGS. These brands will provide you with the highest quality products.
- Make sure that the electrodes are properly cleaned before each use. Cleaning them will help ensure they can cut correctly and avoid potential fires.
- Make sure that the voltage is high enough when using electrodes. Over-voltage can cause damage to your equipment and can also lead to fires. Ensure the voltage is set at the correct level before cutting begins.
- Use a cutting tip designed specifically for electrodeposition lithography (EDL). These tips need a higher voltage than others, resulting in better quality results.
- Always use caution when working with electrodes, and make sure that you follow all safety guidelines when using them. Doing so will help prevent any accidents from happening and will allow you to get the most out of your equipment.
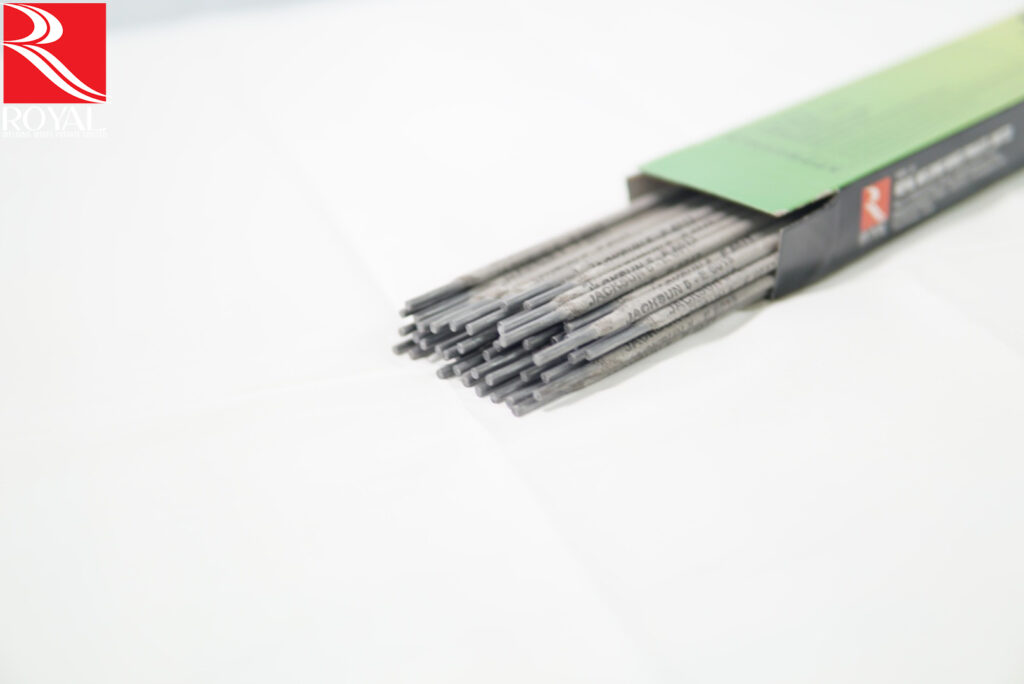
What are the things to consider when choosing to cut electrodes?
Electrodes are one of the most important parts of an electrode electrochemical cell or battery. They are the contact points between the working electrode and the solution.
A good cutting electrode should have the following features:
- Sharpness: The cutting edge of the electrode must be sharp so that it can cut through the solution quickly and easily. This is especially important when working with corrosive or acidic solutions.
- Durability: The electrode’s cutting edge must be durable to withstand repeated use without deteriorating.
- Resistance to wear and tear: The cutting edge of the electrode should resist wear and tear caused by contact with the solution, other electrodes, and other materials.
What types of metals can I use to make Cutting Electrodes?
You can use a few different types of metals to make cutting electrodes. The most common are steel and stainless steel. You can also use copper, aluminum, and brass. Each has its advantages and disadvantages.
Steel is the most common type of metal you’ll find in cutting electrodes. It’s strong and durable, which makes it a good choice for long-term use. However, steel is also heavy and expensive.
Stainless steel is a variation of steel that is resistant to corrosion. It’s also less expensive than steel, but it doesn’t have the same strength or durability.
Copper is another popular choice for cutting electrodes. It’s lightweight and easy to work with, making it a good choice for small projects. However, copper is also weak and susceptible to corrosion.
Aluminum is a softer metal than copper, which makes it less likely to cause damage when cutting wires. Brass is an alloy of copper and zinc, making it stronger than copper and aluminum. However, brass is also more expensive than either of those metals.

What is the biggest mistake that manufacturers make when cutting electrodes?
The biggest mistake manufacturers make when cutting electrodes is not following the correct electrode dimensions.
Not only does this lead to inaccurate cuts, but it can also cause damage to the electrode. Inaccurate electrode cuts can also lead to poor electrical performance and battery life.
What are the advantages of cutting electrodes for my company?
There are many advantages of cutting electrodes for your company.
Some advantages include:
- Reduced electrode disposal costs
- Reduced fabrication time
- Reduced manufacturing costs
- Increased production efficiency
What is the average cost for cutting electrodes?
The average cost for cutting electrodes is around $50-$100.
Conclusion
In this article, we have discussed the different types of cutting electrodes and their uses.
We have also provided tips on how to use them properly so that you get the best performance from them.