Do you know the 7 crucial mistakes in MIG welding? Our expert author shares his knowledge to prevent these mistakes, so your welds are smooth and clean.
Introduction
MIG welding is a popular process that uses a wire passed through a gas shield. The most common mistake welders make using the wrong kind of wire for the project at hand.
This article will discuss seven mistakes MIG welders often make and how to avoid them.
1) Not Knowing the Right Welder
There are a few factors that you should consider when choosing a welder. These include the material you will be welding, the power source you will be using, and the project size.
When welding metal, you will need to consider the type of metal you are welding. You can weld mild steel, aluminum, or stainless steel.
The power source you will be using also affects the type of welding you can do. You can use an electric welder, gas welder, or arc welder.
The project size also affects the type of welding that can be done. You can weld small pieces of metal or large amounts of metal.
2) Choosing the Wrong Gas
Mistakes people make when welding uses the wrong gas. The gas choice is one of the most critical factors in welding success. There are many types of welders; each requires a different kind of gas to perform correctly.
Always consult your welding manufacturer or qualified welding technician if you’re unsure which gas to use. Gas choice is one of the most critical factors in welding success and can make or break a project.

3) Not Keeping a Clean Weld Area
One of the most common mistakes in MIG welding is not keeping a clean weld area. This can happen when you don’t properly clean the area before welding or you don’t clean the weld area correctly after welding.
If you don’t keep a clean weld area, it will become clogged with Weld spatter and slag. This will make it difficult to Weld correctly, and the Weld will likely fail.
Always clean the weld area before and after welding to avoid this problem. Use a wire brush to remove dirt, slag, or metal particles. Then use a degreaser to remove any residual welding materials. Finally, use a water rinse to clean the area thoroughly.
Discover the 7+ Mistakes in MIG Welding and How to Avoid Them! Get the Best Quality MIG Welding Wire Now and Ensure Perfect Welds Every Time!
4) Not Prepping the Spot Before Welding
Common mistakes made in MIG welding are not prepping the spot before welding. When welding metal, it is essential to remove any dirt, rust, or other debris that may be on the surface. This will help ensure a clean weld and prevent any problems.
Another mistake that is often made is not using enough pressure when welding. When pressure is applied to the Weld, it will melt more metal and create a stronger connection. Too much stress can also cause unevenness in the Weld and later problems.
It is essential to take the time to prepare the spot before welding to avoid these mistakes and get quality welds every time.
5) Ignoring Resistance
If you ignore this resistance, you will end up with a weld that is too thin and not strong enough. This can lead to problems with the Welded joint, including cracking and failure.
It is essential to pay attention to the resistance when welding metal together. If you are unsure how to do so, consult a welding instructor or manufacturer’s documentation. Doing so will help you avoid making common mistakes in MIG welding.
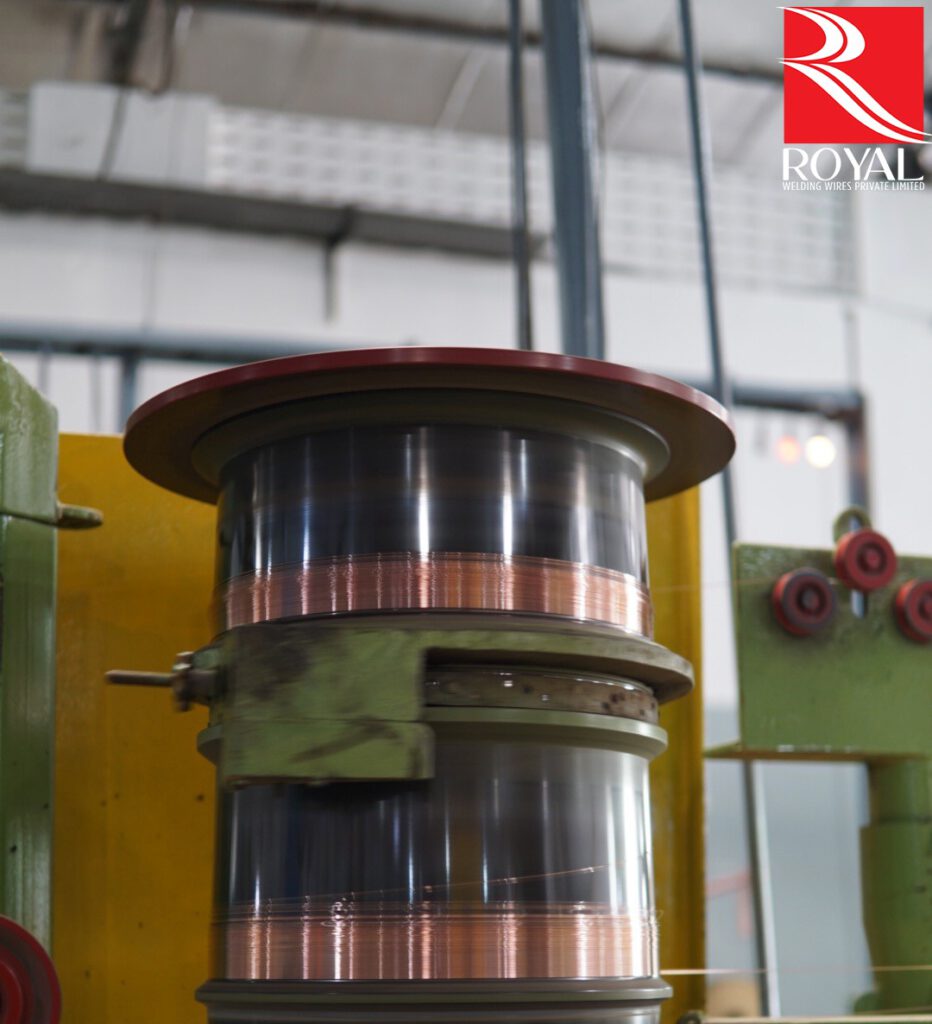
6) Choosing the wrong welding wire
When it comes to welding, there are a few things that you should keep in mind. One of the welders’ most common mistakes is choosing the wrong welding wire.
There are several different welding wire types, each with its specific purpose. For example, the carbon-steel welding wire is used for welding metals with high carbon content, such as stainless steel. It’s also suitable for working with low-alloy steels.
The main benefit of using this type of wire is its relatively low melting point. This means it can be used to weld complex materials without overheating them.
On the other hand, the galvanized steel welding wire is designed specifically for welding galvanized steel. This type of wire has a higher melting point than carbon-steel welding wire, so it’s suitable for welding more difficult metals. It’s also ideal for welding with high-alloy steel.
7) I am not using filler metal.
When welding with MIG (metal-in-metal) welding, it’s essential to use filler metal to prevent heat from building up inside the weld joint. If you don’t use filler metal, the Weld will be weak and may fail.
To make sure your welds are strong, follow these tips:
- Use a filler metal that’s the same thickness as the metal you’re welding. This will help to prevent heat from building up in the weld joint and making it weak.
- Make sure the Weld is clean before you start welding. This will reduce the chances of clogs and other problems.
- Start your Weld by heating both pieces of metal until they’re hot enough to join together. Then, hold them together for a few seconds while you continue to weld them together.
8) I am not using a shielding gas.
When welding with MIG (metal-in-gas) technology, it is essential to use a shielding gas to protect the weld area from the arc and Sparks. Not using a shielding gas can cause significant damage to the weld joint. Here are some tips for using a proper shield gas:
- Always use a quality MIG Welding Shield Gas
- Use a high-purity gas
- Use the correct flow rate

9) I am not maintaining the welder.
Not maintaining the welder can lead to several problems, including poor welds, spatter, and weld quality.
Poor welds can cause structural damage to a car. Spatter can get into people’s eyes and mouths, creating an unsafe environment. And poor weld quality can lead to cracks in the metal that could eventually cause it to fail.
It’s essential to keep your welder in good condition by regularly cleaning it and repairing any damage. Doing so will ensure that your welds are of high quality and that you prevent any safety issues from happening.