In this article, we will discuss the key factors that should be considered when selecting low hydrogen welding electrodes and provide some expert tips and recommendations to help you make an informed decision.
Importance of Low Hydrogen Welding Electrodes
Low hydrogen welding electrodes are essential for ensuring the integrity and longevity of welds in specific applications.
This is because hydrogen in the welding process can cause hydrogen-induced cracking, weakening the weld and reducing its overall strength and durability.
By using low hydrogen welding electrodes, welders can minimize the amount of hydrogen in the welding process and reduce the risk of hydrogen-induced cracking, resulting in more robust, more reliable welds.
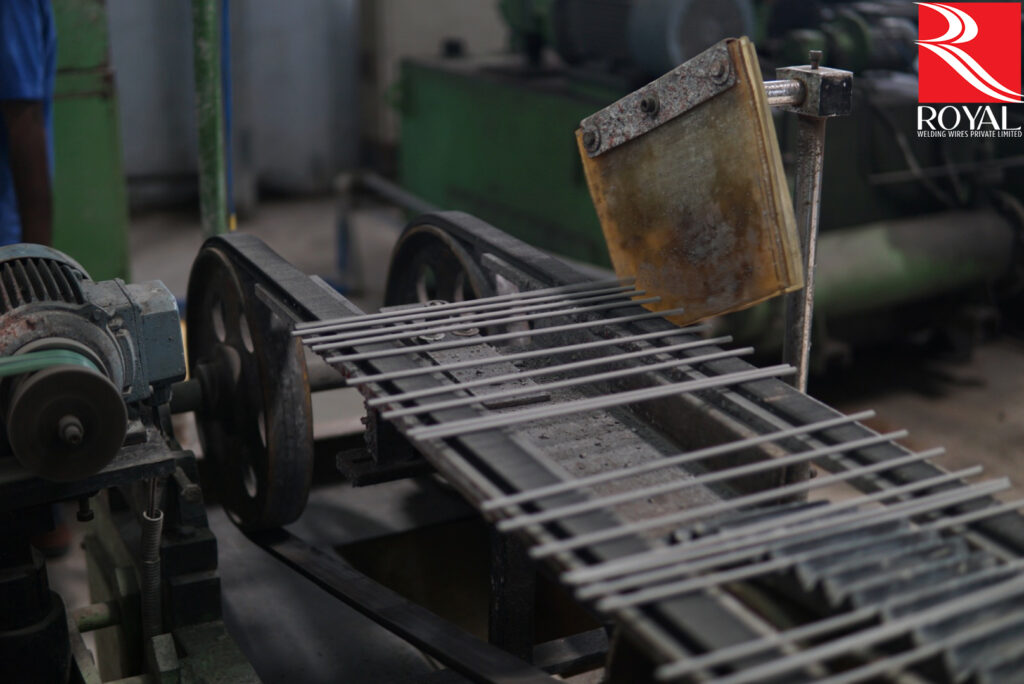
Factors to Consider when Selecting Low Hydrogen Welding Electrodes
When selecting low hydrogen welding electrodes, there are several key factors that should be considered, including:
Welding Position:
Different types of low hydrogen welding electrodes are designed for use in specific welding positions, such as flat, vertical, or overhead. It is important to choose a low hydrogen welding electrode suitable for the position you will be welding.
Welding Current:
The welding current, or the amount of electrical current used in the welding process, can significantly impact the performance of low hydrogen welding electrodes.
Some electrodes are designed for specific welding currents, so it is essential to choose a low hydrogen welding electrode compatible with the welding current you will be using.
Welding Material:
The type of material you will be welding can also influence the selection of low hydrogen welding electrodes.
Different low hydrogen welding electrodes are designed for use with specific materials, such as carbon steel, stainless steel, or aluminum. It is essential to choose a low hydrogen welding electrode suitable for the material you will be welding.
Discover the Benefits of Low Hydrogen Welding Electrodes Today! Get the Expert Advice You Need to Make the Right Choice for Your Project. Shop Now!

Factor | Considerations |
---|---|
Type of metal | Choose a low hydrogen electrode that is compatible with the type of metal being welded. |
Thickness of material | Select an electrode with a sufficient current capacity to handle the thickness of the material. |
Position of weld | Consider the type of electrode and the welding process that is best suited for the position of the weld (e.g. flat, horizontal, vertical, overhead). |
Welding process | Choose an electrode that is compatible with the welding process being used (e.g. shielded metal arc welding, flux-cored arc welding, submerged arc welding). |
Ambient temperature | Select an electrode with a suitable moisture content and diffusible hydrogen level for the ambient temperature. |
Expert Tips and Recommendations
- Choose a reputable brand: Quality is critical regarding low hydrogen welding electrodes. Choosing a reputable brand with a proven track record of producing high-quality, reliable low hydrogen welding electrodes is essential.
- Consult with a welding expert: If you are unsure which low hydrogen welding electrode is best for your specific welding applications, it is a good idea to consult with a welding expert who can provide guidance and recommendations based on your specific needs and requirements.
- Try before you buy: It is always a good idea to try out different low-hydrogen welding electrodes before purchasing. This will allow you to see how they perform in your specific welding applications and help you make an informed decision.
Conclusion:
In conclusion, low hydrogen welding electrodes are essential for welders who want to produce high-quality welds with minimal risk of cracking or other defects.
By considering the factors discussed in this article and following the expert tips and recommendations provided, you can choose the right low hydrogen welding electrode for your specific welding applications and maximize the performance and reliability of your welds.