Choosing the right electrode for your welding process is crucial to achieving a robust and high-quality weld. The electrode is the component of the welding process that melts and fuses the metal, and there are many different types and materials to choose from.
In this article, we will explore How we can maximize welding performance with high-quality electrodes?
How to Choose the Right Electrode for Your Welding Process
When it comes to welding, the choice of the electrode plays a crucial role in the success of the process.
There are several factors to consider when selecting the right electrode for your welding process, including the type of metal being welded, the welding position, and the desired strength and appearance of the finished weld.
- Carbon steel electrodes: for welding low carbon steels, suitable for all welding positions.
- Stainless steel electrodes: for welding stainless steel and other high alloy steels, available in coated and uncoated forms.
- Aluminum electrodes: for welding aluminum and its alloys, suitable for all welding positions.
- Nickel electrodes: for welding nickel and its alloys, suitable for all welding positions.
- Copper electrodes: for welding copper and its alloys, suitable for all welding positions.

How can I maximize welding performance with high-quality electrodes?
Welding is a critical process in various industries, and the quality of the welds depends on several factors, including the quality of the welding electrodes used.
High-quality electrodes can significantly improve welding performance by providing consistent and stable arcs, producing minimal spatter, and producing solid and durable welds.
Here are some tips to help you maximize welding performance with high-quality electrodes:
- Choosing the Right Electrode for Your Welding Process: Different welding processes require different electrodes. For example, the electrode for gas metal arc welding (GMAW) is not the same as the electrode for shielded metal arc welding (SMAW). Selecting the right electrode for your welding process will ensure optimal performance and results.
- Storing and Handling Electrodes Properly to Maintain Quality: Electrodes can be damaged by exposure to moisture, extreme temperatures, and other factors. Proper storage and handling are crucial to maintain the quality of the electrodes and ensure they perform as expected.
- The Role of Electrode Diameter and Length in Welding Performance: The diameter and length of the electrode can affect the welding performance. For example, smaller diameter electrodes can help increase welding speed, while more extended electrodes can provide more stability and control.
- The Importance of Regularly Inspecting and Replacing Electrodes: Over time, electrodes can become worn or damaged, negatively impacting welding performance. It’s essential to inspect and replace electrodes to ensure optimal performance regularly.
- Using the Correct Welding Technique for Optimal Electrode Performance: The correct welding technique can ensure that the electrode is used most efficiently and effectively, resulting in improved welding performance.
- The Impact of Welding Environment on Electrode Performance: The environment in which the welding takes place can also affect electrode performance. For example, welding in windy or damp conditions can negatively impact electrode performance.
- Optimizing Welding Power Settings for High-Quality Electrodes: Properly adjusting the welding power settings can help maximize the performance of high-quality electrodes.
- The Benefits of Using Premium Electrodes for Superior Welding Results: Using premium quality electrodes can provide superior welding results, as they are made to stricter quality standards and are more consistent in performance.
- The Role of Pre-weld and Post-weld Cleaning in Maximizing Electrode Performance: Cleaning the workpiece before and after welding can help remove any contaminants that may affect electrode performance.
- The Importance of Proper Training and Certification in Using High-Quality Electrodes: Proper training and certification in high-quality electrodes can ensure that the welder knows how to use the electrodes correctly and safely, which can help maximize welding performance.
By following these tips, you can ensure that you are using high-quality electrodes and maximizing welding performance.
Upgrade your welding performance today with our high-quality electrodes! Our electrodes will ensure your work is durable, efficient and cost-effective. Contact us now for more information on the best electrodes for your needs. Order your electrodes today and take the first step to achieving professional welding results.
Storing and Handling Electrodes Properly to Maintain Quality
Proper storage and handling of electrodes are crucial to maintain their quality and ensure they perform optimally during welding.
The following are some tips for storing and handling electrodes:
- Store electrodes in a dry location, as moisture can cause them to deteriorate and become unusable.
- Keep electrodes in their original packaging until ready to use to protect them from damage and contamination.
- Do not expose electrodes to extreme temperatures, affecting their chemical composition and weakening the finished weld.
- Use the correct storage container, such as a dry and ventilated container, to protect electrodes from moisture and other environmental factors.
- Handle electrodes with care to avoid breaking or damaging the tips.
- Rotate your inventory of electrodes, using the oldest stock first, to ensure that they are used before their expiration date.
Role of Electrode Diameter
The diameter of an electrode plays an essential role in the welding process as it affects the amount of heat generated and the size of the weld.
In general, larger-diameter electrodes generate more heat and produce more significant welds, while smaller-diameter electrodes create less heat and produce more minor welds.
- Larger Diameter Electrodes: provide higher heat input, and create more comprehensive, more profound, and more robust welds, typically used for heavy-duty welding.
- Smaller Diameter Electrodes: provide lower heat input and create smaller, less deep, and less strong welds, typically used for precision welding.
- Choosing the correct diameter electrode: depends on the application, thickness of metal, welding position, desired strength, and appearance of the finished weld.
Role of Length in Welding Performance
The length of a weld is crucial because it affects:
- Affects the strength of the weld: Longer welds tend to be stronger than shorter ones due to increased surface area for fusion.
- Determines the amount of heat input: A longer weld requires more heat input, which can affect the quality of the weld and the surrounding metal.
- Can lead to warping and distortion: Longer welds can cause more warping and distortion of the metal due to the high heat input.
- Can affect the cost of the welding process: Longer welds may require more materials and labor, increasing the overall cost.
- Can influence the final aesthetic appearance of the weld: Longer welds may have a more significant visible impact on the final appearance of the workpiece.
- Can affect the fatigue resistance of the weld: Longer welds may have better fatigue resistance as they tend to be stronger, but they may also be more prone to cracking if they are not done correctly.
Upgrade your welding performance today with our high-quality electrodes! Our electrodes will ensure your work is durable, efficient and cost-effective. Contact us now for more information on the best electrodes for your needs. Order your electrodes today and take the first step to achieving professional welding results.
Importance of Regularly Inspecting and Replacing Electrodes
- Ensure quality and safety: Regular inspection and replacement of electrodes ensure that they are in good condition and perform well during the welding process, reducing the risk of accidents or defects.
- Improve efficiency: Worn or damaged electrodes can result in poor weld quality, lower productivity, and increased downtime. Regular inspection and replacement of electrodes can prevent these issues and improve overall efficiency.
- Maintain consistency: Regularly inspecting and replacing electrodes helps maintain consistency in the finished welds, ensuring that the same quality is achieved every time.
- Extend equipment life: Properly maintaining and replacing electrodes can help extend the welding equipment’s life.
- Cost-effective: Regularly inspecting and replacing electrodes can save money in the long run by reducing the need for costly repairs and downtime.
In summary, regularly inspecting and replacing electrodes is essential to ensure quality and safety, improve efficiency, maintain consistency, extend equipment life, and be cost-effective.
Correct Welding Technique for Optimal Electrode Performance
Correct welding technique is essential for achieving optimal electrode performance. The following are some key factors to consider when welding with electrodes:
- Proper preparation of the base metal and the electrode is crucial for achieving a good weld. The base metal should be cleaned of contaminants, and the electrode should be appropriately stored and handled to prevent damage.
- The correct electrode size and type should be selected based on the welded metal and welding conditions.
- The correct welding technique should be used based on the electrode type and welding conditions. For example, the method used for welding with a coated electrode will be different than that used with a bare electrode.
- The welding speed and current should be adjusted to achieve the desired weld quality and penetration.
- Proper post-weld cleaning and inspection should ensure that the weld is free of defects and has the desired properties.
Following these guidelines can ensure optimal electrode performance and achieve high-quality welds.
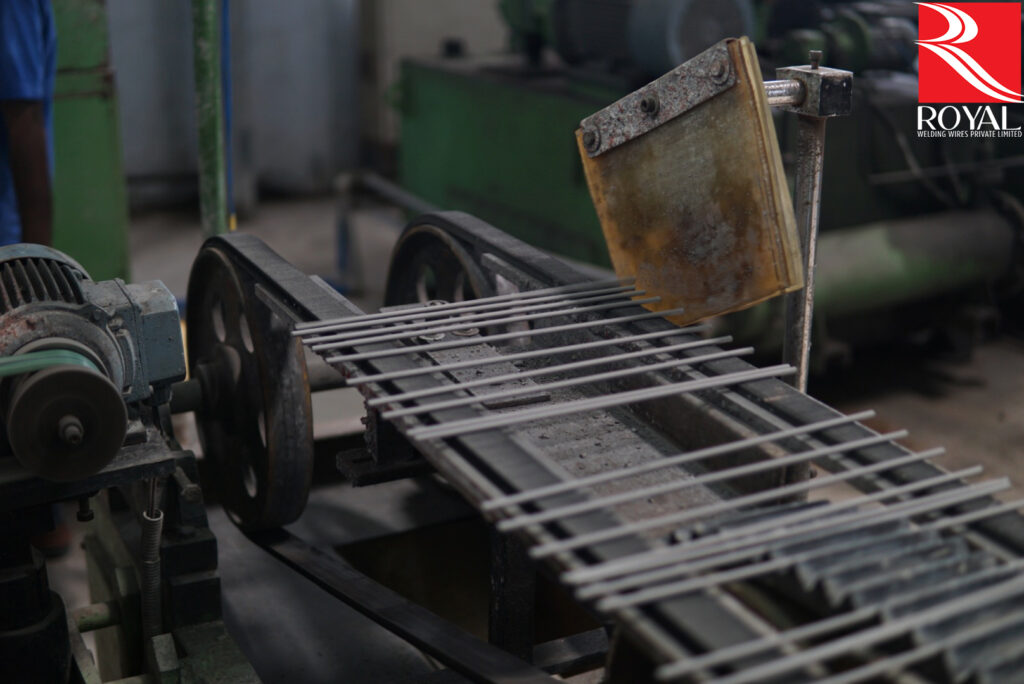
Impact of Welding Environment on Electrode Performance
Impacts of Welding Environment on Electrode Performance:
- Poor weld quality
- Electrode corrosion
- Electrode damage
- Brittle or soft electrode
- Reduced electrode conductivity
- Reduced electrode lifespan
- Reduced efficiency of the welding process
- Increased cost due to frequent replacement of electrodes.
Optimizing Welding Power Settings for High-Quality Electrodes
Optimizing power settings when using high-quality electrodes is essential for achieving a robust and high-quality weld.
Factors to consider include amperage (related to metal thickness), voltage (strength of the arc), and duty cycle (amount of time the power source can be used without cooling down).
It’s essential to understand the welding process’s specific requirements and the electrodes’ properties.
Benefits of Using Premium Electrodes for Superior Welding Results
Benefits of Using Premium Electrodes for Superior Welding Results:
- Improved weld quality
- Increased efficiency
- Longer electrode lifespan
- More excellent resistance to corrosion and wear
- Enhanced conductivity
- Greater tolerance to harsh welding environments
- Increased productivity and cost savings in the long run.
Frequently Asked Questions (FAQ)
Q: How can cleaning the electrode and the workpiece surface before welding can help?
Q: How to prevent corrosion on electrodes?
Q: How to determine the end of life of an electrode?
Q: How to handle and store high-quality electrodes correctly?
Last Word
To achieve superior welding results with high-quality electrodes, it is crucial to use the right type, keep them in good condition, clean both the electrode and workpiece surface, use the right technique, and use a power source specifically designed for high-quality electrodes.
Proper storage and handling of electrodes also play a key role in maintaining their quality.
By following these steps, welders can ensure they’re getting the most out of their high-quality electrodes and achieving exceptional welding results.