Are you tired of mediocre welding results that just don’t cut it? Step aside basic rods because low hydrogen welding rods are here to shake up the game.
These bad boys improve weld quality and increase durability, so you can weld like a boss and leave your competition in the dust.
So, put down those old rusty rods and join the future of welding with low hydrogen rods.
How Low Hydrogen Welding Rods Minimize Porosity and Cracking?
Low hydrogen welding rods are specifically designed to minimize porosity and cracking in the welds. Here’s how:
- Hydrogen Control: Low hydrogen rods are designed to control the amount of hydrogen in the weld. Low hydrogen rods prevent porosity and cracking in the weld by maintaining hydrogen.
- Special Coating: Low hydrogen rods have a special coating that reduces the amount of hydrogen that can penetrate the weld. This coating helps keep the hydrogen out of the weld metal, resulting in more robust, durable welds.
- Dry and Controlled Environment: Low hydrogen welding typically requires a dry and controlled environment. This can be achieved by using a low hydrogen welding process such as Shielded Metal Arc Welding (SMAW) or Gas Tungsten Arc Welding (GTAW), which helps reduce humidity and moisture in the air. This helps to minimize the amount of hydrogen that can be absorbed by the welding rod and ultimately reduces the chance of porosity and cracking in the weld.
- Improved Weld Quality: By controlling the porosity and cracking, low hydrogen rods result in welds that are stronger, more durable, and have a higher overall quality. This means less rework and less wasted time and resources in the long run.
- Greater Versatility: Low hydrogen rods can be used in various welding applications and on different materials, making them a versatile choice for any welding project.
Learn More: What factors should be considered when selecting low hydrogen welding electrodes?

Role of Low Hydrogen Welding Rods in Improving Tensile Strength
Low hydrogen welding rods play a crucial role in improving the tensile strength of welds. Here are a few ways in which they achieve this:
- Hydrogen Control: Low hydrogen rods control the amount of hydrogen in the weld, which helps prevent porosity and cracking. This results in a stronger, more durable weld with better tensile strength.
- Special Coating: Low hydrogen rods have a special coating that reduces the amount of hydrogen that can penetrate the weld. This coating helps keep the hydrogen out of the weld metal, resulting in more robust, durable welds with improved tensile strength.
- Controlled Welding Environment: Low hydrogen welding requires a dry and controlled environment which helps to minimize the amount of hydrogen that can be absorbed by the welding rod. This ultimately helps in reducing the chance of porosity and cracking in the weld, leading to improved tensile strength.
- Reduced Porosity: Low hydrogen rods help minimize porosity, improving the weld’s overall strength and increasing the tensile strength.
Comparing Low Hydrogen Welding Rods to Traditional Welding Techniques
Low Hydrogen Welding Rods | Traditional Welding Techniques | |
---|---|---|
Hydrogen Control | Yes | No |
Special Coating | Yes | No |
Controlled Welding Environment | Yes | No |
Improved Weld Quality | Yes | No |
Versatility | Yes | No |
Applications of Low Hydrogen Welding Rods in Improving Weld Quality and Durability
Low hydrogen welding rods are used in various applications to improve weld quality and durability by controlling hydrogen levels.
- Construction
- Shipbuilding
- Oil and gas
- Power generation
- etc
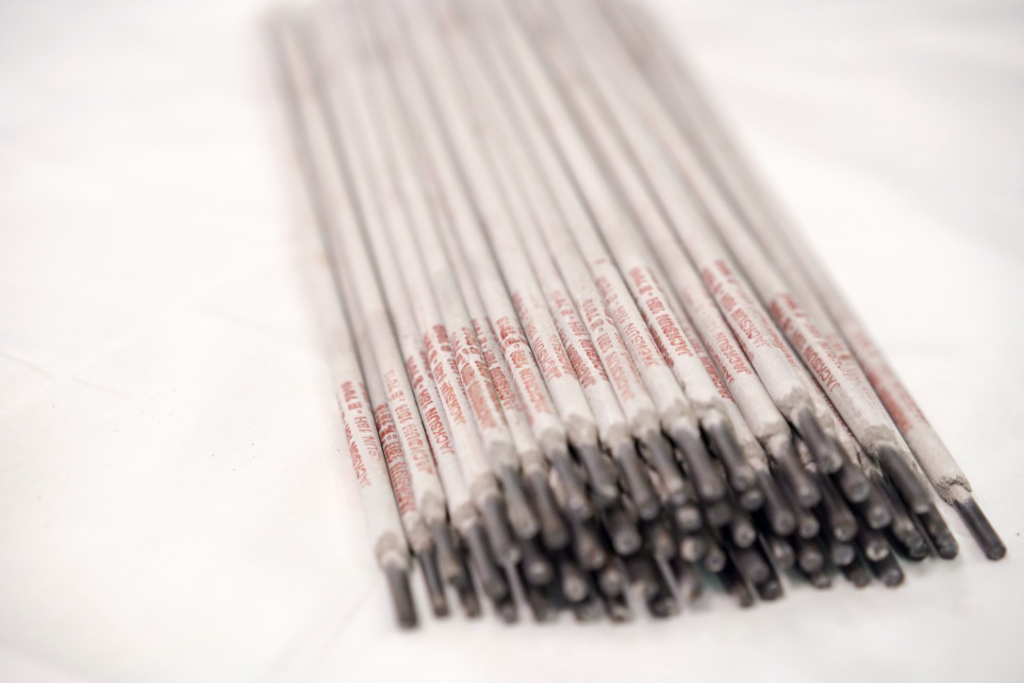
Future of Welding: Low Hydrogen Welding Rods and Emerging Technologies
Low hydrogen welding rods have been widely used in the industry for many years and have proven effective in improving weld quality and durability. As the technology continues to evolve, new and emerging technologies are also being developed to enhance the performance of low hydrogen welding rods even further. Some of these technologies include:
- Automation and Robotics: Automation and robotics are being used to improve the efficiency and precision of welding processes. This can help to reduce the need for skilled labor and decrease the risk of human error.
- Advanced Coatings: New and advanced coatings are being developed to reduce further the amount of hydrogen penetrating the weld. This can help to improve the strength and durability of the weld.
- Non-Conventional Welding Processes: Non-conventional welding processes, such as laser welding and plasma welding, are being developed and used to improve the efficiency and precision of welding. These processes can also help to reduce the amount of heat and distortion in the weld.
- Real-time monitoring: Real-time monitoring and data analysis are being used to improve the understanding of the welding process and to identify potential issues. This can help to improve the quality and consistency of the weld.
- Artificial Intelligence: Artificial intelligence and machine learning are being used to optimize the welding process and to predict and prevent defects in the weld.
Frequently Asked Questions (FAQ)
Q: How does the coating on low hydrogen rods prevent hydrogen penetration?
Q: What type of environment is required for low hydrogen welding?
Q: Can low hydrogen welding rods be used on different materials?
Q: How do low hydrogen welding rods compare to other welding rods?
Q: Are any safety precautions to be taken while using low hydrogen rods?
Last Word
Low hydrogen welding rods are essential to improve weld quality and durability. By controlling hydrogen levels, using special coatings, and creating a controlled environment, these rods produce more robust and durable welds.
Not only do they save time and money by reducing rework, but they are also versatile in many industries. To ensure the best results, always follow safety precautions and manufacturer instructions.