Are you tired of dealing with the frustration and disappointment of using wet welding electrodes? Well, have no fear! This guide teaches you the ins and outs of keeping your welding electrodes dry and ready for action.
Say goodbye to weak, porous welds and hello to substantial, professional results. Get ready to become a welding electrode storage pro and impress all your friends with your newfound knowledge.
Effects of Moisture on Welding Electrodes
Moisture can significantly impact the performance and quality of welding electrodes. When welding electrodes become contaminated with water, it can cause several problems, including:
- Reduced Arc Stability: Moisture can cause the arc to become unstable, resulting in poor weld quality and an increased risk of porosity.
- Reduced Weld Strength: Moisture can weaken the weld and reduce strength and flexibility. This can make the weld more prone to cracking and failure.
- Increased Spatter: Moisture can cause increased spatter during welding, resulting in a messy and difficult-to-clean weld surface.
- Reduced Welding Speed: Moisture can slow down the welding process and make it more challenging to achieve the desired results.
- Reduced Shelf Life: Welding electrodes exposed to moisture have a shorter shelf life and need to be used or discarded sooner.
- Increased Risk of Welding Defects: Moisture can lead to a higher risk of defects such as porosity, lack of fusion, and undercutting.
Techniques for Drying Wet Welding Electrodes
A few techniques can be used to dry wet welding electrodes and remove moisture from the electrodes. Some of the most common methods include:
- Oven Drying: This is a standard method for drying wet welding electrodes. The electrodes are placed in a low-heat oven (around 200-250°F) for some time (usually 1-2 hours). This method can effectively remove moisture, but it can also cause the electrodes to degrade if the temperature is too high.
- Heating Lamp: A heating lamp can dry wet welding electrodes. The electrodes are placed close to the light and left until dry. This method can be less effective than oven drying, but it is less risky in degrading the electrodes.
- Desiccant: A desiccant is a moisture-absorbing material used to dry wet welding electrodes. Desiccants such as silica gel can be placed inside a container with wet electrodes until the desiccant has absorbed the moisture. This method is relatively effective, but it May not remove all the water from the electrodes.
- Air-Drying: This method involves simply leaving the wet welding electrodes out in a dry environment until they are dry. This method can be effective, but it can also take a long time for the electrodes to dry completely, depending on the humidity level.

Proper Handling & Transport of Welding Electrodes
Proper handling and transporting welding electrodes are crucial to ensuring they remain dry and usable.
Here are some tips to help with the proper handling and transport of welding electrodes:
- Keep electrodes in a dry container: Always store welding electrodes in an airtight and moisture-proof dry container. This will help to keep the electrodes dry and protect them from moisture during transport.
- Avoid exposure to water: Avoid exposing welding electrodes to moisture or high humidity during transportation. Keep them away from sources of moisture such as rain or snow, and avoid transporting them in a damp vehicle or trailer.
- Handle with care: Always handle welding electrodes with care to prevent damage. Dropping or mishandling the electrodes can cause them to break or become contaminated with dirt or debris.
- Use proper packaging: When transporting welding electrodes, use adequate packaging to protect them from damage. Use packaging materials such as foam, bubble wrap, or paper to cushion the electrodes and prevent them from moving around during transport.
- Keep welding electrodes upright: Always transport welding electrodes upright and in a good position. This will help to prevent them from becoming contaminated with dirt or debris.
How to Store Welding Electrodes for Long-term Use?
Proper storage of welding electrodes is crucial to ensuring that they remain dry and usable for long-term use.
Here are some tips to help with the proper storage of welding electrodes:
- Keep electrodes in a dry environment: Always store welding electrodes in a dry climate free from moisture and humidity. A dry and cool place like a storage room or a cabinet is ideal.
- Use airtight and moisture-proof containers: Use airtight and moisture-proof containers to store welding electrodes. This will help to keep the electrodes dry and protect them from moisture.
- Store electrodes in a vertical position: Always store welding electrodes in an upright position; this will help prevent them from becoming contaminated with dirt or debris.
- Use desiccant: You can also use desiccant or humidity indicator cards to detect and absorb moisture. Place them inside the container with the electrodes.
- Use proper labeling: Properly label the storage container with the electrode type and the date when it was stored; this will help keep track of the storage and usage of the electrodes.
- Regularly inspect the electrodes: Regularly check the electrodes for signs of moisture or other damage. If you notice any issues, discard the electrodes or use them as soon as possible.
Tips for Maintaining a Dry Welding Environment
- Keep the welding area well-ventilated to promote air circulation and reduce humidity.
- Use air conditioning or dehumidifiers to control the humidity in the welding area.
- Use moisture-absorbing materials such as desiccants to absorb moisture in the air.
- Avoid welding in damp or humid environments, and try to schedule welding for dry and sunny days.
- Use a welding enclosure or tent to create a controlled environment for welding.
- Regularly check the humidity level in the welding area with a hygrometer.
- Use proper storage for welding materials and equipment to keep them dry.
- Inspect and maintain welding equipment, including torches and hoses, to ensure they are not leaking or introducing moisture into the welding area.
- Keep the welding area clean and debris-free, which can hold water and make the environment more humid.
- Educate yourself and your team on the importance of a dry welding environment and the steps to maintain one.
Common Mistakes to Avoid when Keeping Welding Electrodes Dry
Here is the common mistakes to avoid:
- Not storing electrodes in airtight and moisture-proof containers.
- Not using desiccant or humidity indicator cards to absorb moisture.
- Not regularly inspecting and testing electrodes for water.
- Need to handle and transport electrodes properly to avoid exposure to water.
- Not storing electrodes in a vertical position to prevent contamination with dirt or debris.
- Not keeping the welding area well-ventilated and allowing humidity to build up.
- Using proper packaging to protect electrodes during transport.
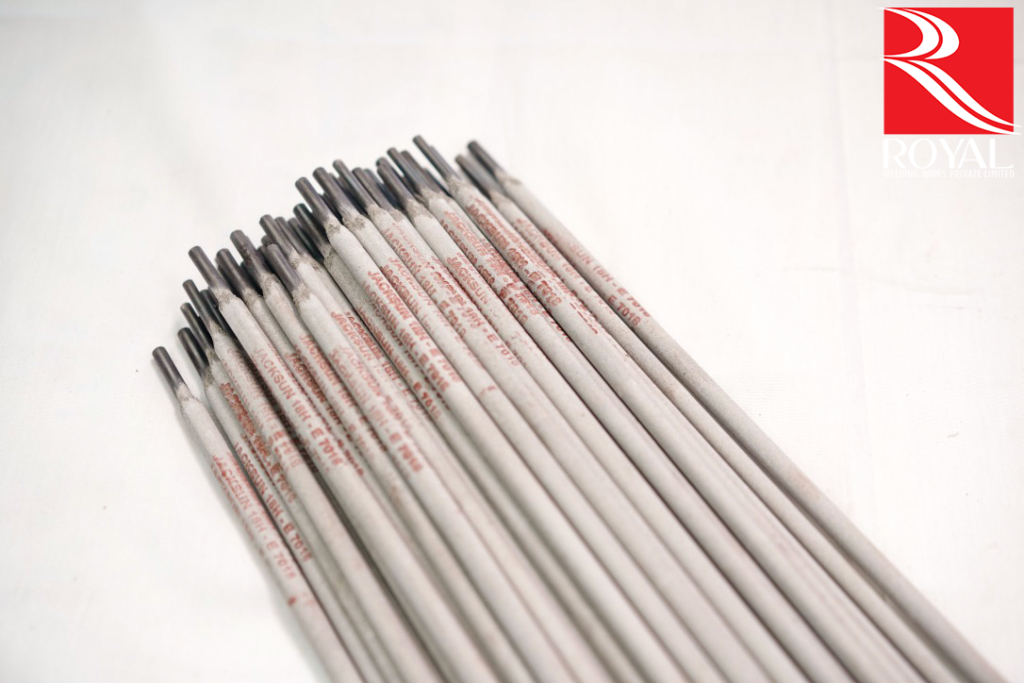
How to Salvage Moisture-Contaminated Welding Electrodes
Salvaging moisture-contaminated welding electrodes can be tricky, but it’s not impossible.
Here are some tips to help you salvage moisture-contaminated welding electrodes:
- Oven drying is a standard method for drying out moisture-contaminated welding electrodes. The electrodes are placed in a low-heat oven (around 200-250°F) for some time (usually 1-2 hours). This method can effectively remove moisture, but it can also cause the electrodes to degrade if the temperature is too high.
- Heating Lamp: A heating lamp can dry moisture-contaminated welding electrodes. The electrodes are placed close to the light and left until dry.
- Desiccant: A desiccant is a moisture-absorbing material used to dry moisture-contaminated welding electrodes. Desiccants such as silica gel can be placed inside a container with wet electrodes until the desiccant has absorbed the moisture.
- Air-Drying: This method involves simply leaving the moisture-contaminated welding electrodes out in a dry environment until they are dry.
- Discard heavily contaminated electrodes: If the electrodes are heavily contaminated with moisture, it may be best to discard them and use new ones.
Frequently Asked Questions (FAQ)
Q: Why is it essential to keep welding electrodes dry?
Q: What are the common causes of moisture contamination in welding electrodes?
Q: What are the proper storage techniques for welding electrodes?
Q: Can wet welding electrodes be salvaged?
Q: How often should I inspect my welding electrodes for moisture?
Last Word
In conclusion, keeping welding electrodes dry is essential to ensuring high-quality welds and avoiding problems caused by moisture contamination.
Proper storage techniques, handling, transport methods, and maintaining a dry welding environment can help keep welding electrodes dry.