Stainless steel is a popular material used in various industries such as construction, automotive, and aerospace due to its high strength and corrosion resistance.
Welding is commonly used to join stainless steel components, and welding electrodes play a crucial role in this process.
This article will discuss the various aspects of stainless steel welding electrodes.
What are the electrodes used for SS welding?
Electrodes are consumable components in welding to create an electric arc between the electrode and the workpiece. The heat generated by the arc melts the base metal, which fuses with the electrode to form a welded joint.
For stainless steel welding, electrodes made of a specific type of stainless steel alloy are used. These electrodes have a coating that shields the weld pool from atmospheric gases and prevents the formation of oxides, which can cause defects in the weld.
Types of Welding Electrodes for Stainless Steel
Various types of welding electrodes for stainless steel are classified according to their composition and coating.
The most common types are:
- E308L: This is a low-carbon electrode with a high chromium and nickel content. It is suitable for welding austenitic stainless steels such as 304 and 304L.
- E309L: This electrode is designed for welding dissimilar metals such as stainless steel to carbon or low-alloy steel. It has a higher carbon content than E308L and is suitable for welding thicker sections.
- E316L: This electrode has a higher molybdenum content than E308L, making it suitable for welding corrosion-resistant austenitic stainless steels such as 316 and 316L.
Factors to Consider when Choosing Welding Electrodes
When choosing welding electrodes for stainless steel, several factors should be considered, such as:
- Base metal composition: The electrode should be selected based on the composition of the base metal to ensure compatibility and optimal welding performance.
- Joint design and fit-up: The electrode size and type should be chosen based on the joint design and fit-up to ensure proper penetration and weld quality.
- Welding position: Electrodes are designed for specific welding positions, such as flat, horizontal, vertical, and overhead. The electrode should be selected based on the intended welding position.
Welding Techniques for Stainless Steel Welding Electrodes
Stainless steel welding electrodes can be welded using various techniques, such as shielded metal arc welding (SMAW), gas tungsten arc welding (GTAW), and gas metal arc welding (GMAW). Each technique has its advantages and disadvantages and is suitable for specific applications.
Upgrade your stainless steel welding with our premium electrodes! Contact us now to choose the perfect stainless steel welding electrode for optimal welding performance and quality.
Mistakes to Avoid When Using Stainless Steel Electrodes
To ensure optimal welding performance and quality, several mistakes should be avoided when using stainless steel welding electrodes, such as:
- Choosing the wrong electrode: Using the wrong electrode can result in poor penetration, porosity, and weld defects.
- Incorrect storage and handling: Improper storage and handling of electrodes can cause moisture absorption, leading to cracking and porosity.
- Inadequate pre-cleaning: Proper pre-cleaning of the base metal is essential to ensure optimal weld quality and prevent contamination.
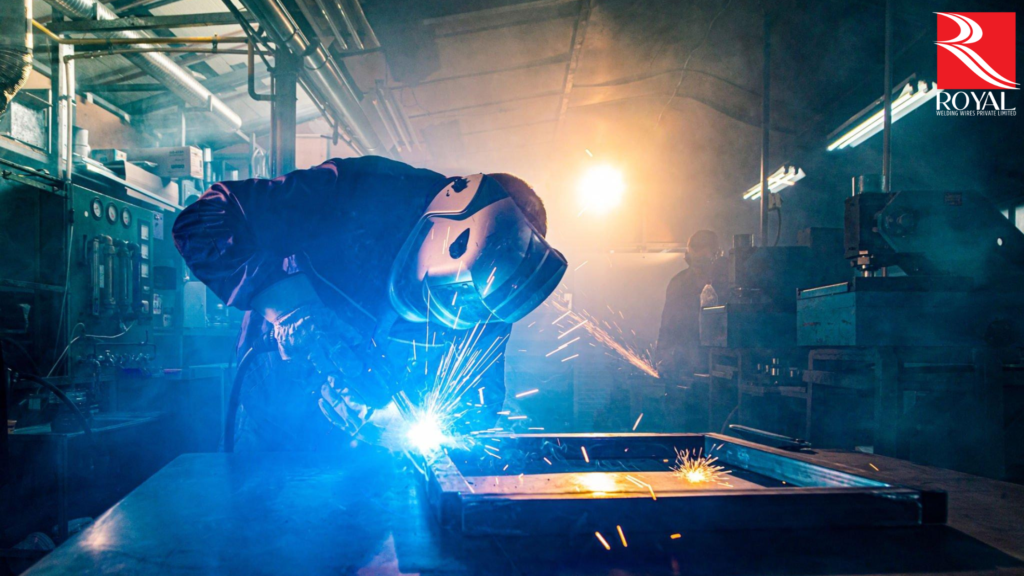
Frequently Asked Questions
Can I use the same electrode for welding different grades of stainless steel?
Can I reuse electrodes?
What is the recommended storage condition for electrodes?
Conclusion
Choosing the right electrode for stainless steel welding is crucial for achieving optimal welding performance and quality. Factors such as the base metal composition, joint design and fit-up, and welding position should be considered when choosing the electrode type and size. Proper storage and handling, adequate pre-cleaning of the base metal, and avoiding common mistakes are essential to ensure optimal welding results.