Welding has been essential for centuries to join metal parts and structures.
Whether you’re an experienced welder or a novice, maximizing your welding potential requires a deep understanding of the available electrode materials and their advantages and disadvantages.
Choosing the suitable electrode material can make all the difference in the quality and durability of your welds.
This article will explore the pros and cons of various welding electrode materials, including carbon steel, stainless steel, cast iron, aluminum, and nickel.
By the end of this article, you’ll better understand which electrode material is best suited for your welding project and how to maximize your welding potential. So, let’s dive in!
Introduction to Welding Electrodes
Welding electrodes are essential components in welding, creating a solid and durable bond between metal parts.
Simply put, a welding electrode is a metal wire with a flux coating used to conduct electricity and create an arc between the electrode and the metal being welded.
This arc produces intense heat that melts the metal and fuses it.
Types of Welding Electrode Materials
Several types of welding electrode materials are available in the market, each with unique properties and applications. Common welding electrode materials include carbon steel, stainless steel, cast iron, aluminum, and nickel.
Carbon steel electrodes
Carbon steel electrodes are the most widely used for their versatility and affordability. They are suitable for welding low to medium-carbon steels and can be used in all welding positions.
stainless steel electrodes
On the other hand, stainless steel electrodes are explicitly designed for welding stainless steel and are ideal for high-temperature applications. They are also resistant to corrosion and oxidation, making them suitable for welding in harsh environments.
Cast iron electrodes
Cast iron electrodes are best suited for repairing or joining cast iron parts. They are designed to produce a soft, malleable weld that can be easily machined.
Aluminum electrodes
Aluminum electrodes are designed for welding aluminum and aluminum alloys, typically used to construct aircraft and other lightweight structures. They are also suitable for welding other non-ferrous metals such as copper and brass.
nickel electrodes
Finally, nickel electrodes are designed for welding high nickel alloys and can withstand extreme temperatures and corrosive environments. They are often used in the chemical and petrochemical industries.
Upgrade your welding skills with the right electrode material. Explore our comprehensive table of pros and cons for each material and start welding like a pro. Browse now and get the perfect electrode for your welding needs!
Pros and Cons of Carbon Steel Electrodes
Carbon steel electrodes are the most commonly used welding electrodes due to their versatility and affordability.
Here are some of the pros and cons of using carbon steel electrodes:
Pros | Cons |
---|---|
Cost-effective | Limited strength |
Versatile | Susceptible to cracking |
High penetration | Limited resistance to corrosion |
Easy to use | Limited versatility in high-temperature |
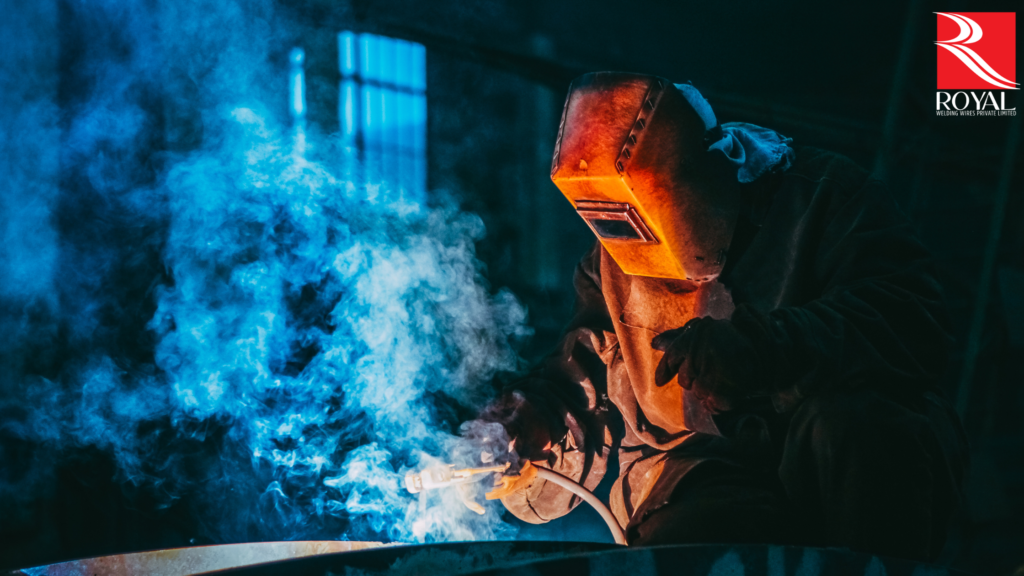
Pros and Cons of Stainless Steel Electrodes
Stainless steel electrodes are popular in welding applications due to their excellent corrosion resistance, high strength, and versatility.
However, they also have some drawbacks that welders need to consider.
This article will discuss the pros and cons of stainless steel electrodes.
Pros | Cons |
---|---|
High resistance to corrosion and oxidation | May have a higher upfront cost than other electrode types. |
High strength and durability | May require preheating or post-weld heat treatment in specific applications. |
Suitable for use in high-temperature environments | Can be more challenging to use and may require more skill from the welder |
Versatile and can be used on a wide range of materials | May not be suitable for certain types of metals. |
Leaves a clean, aesthetically pleasing weld | May produce more smoke and fumes compared to other types of electrodes. |
Can create solid and long-lasting welds | Require careful storage to prevent contamination and maintain quality. |
Resistant to wear and tear | May require special equipment for welding certain types of stainless steel. |
Pros and Cons of Cast Iron Electrodes
Cast iron electrodes are a popular welding choice for repairing or joining cast iron materials.
They are designed to withstand the high temperatures and thermal shock associated with welding cast iron, and can provide a strong and durable weld.
However, as with any welding process, there are both pros and cons to using cast iron electrodes.
Pros | Cons |
---|---|
Versatile: Can be used on various cast iron materials | High skill level required to produce quality welds. |
Cost-effective: Typically more affordable than other types of electrodes | Pre-weld preparation is essential and can be time-consuming. |
Solid and durable welds | Brittle welds can occur if not used properly. |
Low spatter: Produces less spatter compared to other welding processes | Limited use: Primarily designed for use on cast iron materials. |
It can be used for repairs and joining cast iron materials | May not be suitable for welding other types of metals. |
Pros and Cons of Aluminum Electrodes
Aluminum electrodes are a popular choice for welding aluminum materials, as they are designed to create strong and durable welds. However, as with any welding process, there are both pros and cons to using aluminum electrodes.
Pros | Cons |
---|---|
High strength: Creates strong and durable welds | Can be more challenging to use and may require more skill from the welder. |
Versatility: Can be used on a variety of aluminum alloys | May require special storage and handling to prevent contamination and maintain quality. |
Low spatter: Produces less spatter compared to other welding processes | May require pre-weld preparation, such as cleaning and degreasing. |
High conductivity: Has high electrical conductivity, making it ideal for welding aluminum | May have a higher upfront cost compared to other types of electrodes. |
It can create clean and aesthetically pleasing welds | May not be suitable for welding other types of metals. |
Resistant to corrosion and oxidation | May produce more smoke and fumes compared to other types of electrodes. |
Suitable for use in high-temperature environments | May require the use of a shielding gas. |
Pros and Cons of Nickel Electrodes
Nickel electrodes are a popular welding choice for various applications, including welding of nickel-based alloys, dissimilar metals, and even stainless steel. They are designed to create solid, durable welds resistant to corrosion and high temperatures. However, as with any welding process, there are both pros and cons to using nickel electrodes.
Pros | Cons |
---|---|
Versatility: Can be used to weld a wide range of materials, including nickel-based alloys, dissimilar metals, and stainless steel | May have a higher upfront cost compared to other types of electrodes. |
Corrosion-resistant: Creates welds that are highly resistant to corrosion and oxidation | May require special storage and handling to prevent contamination and maintain quality. |
High-temperature resistance: Suitable for use in high-temperature environments | May produce more fumes compared to other types of electrodes. |
Creates solid and durable welds | May require pre-weld preparation, such as cleaning and degreasing. |
Suitable for dissimilar metal welding but | May require more skill from the welder. |
Can produce high-quality, aesthetically pleasing welds | May require a shielding gas. |
Can be used for repair work | Limited use: Primarily designed for welding nickel-based materials. |
Choosing the Right Electrode Material for Your Welding Project
When it comes to welding, selecting the appropriate electrode material is crucial to the success of your project.
The electrode material not only affects the quality and strength of the weld but also impacts the ease of use and overall cost of the process.
With so many options available, choosing the suitable electrode material for your specific welding application can be challenging.
Here are some factors to consider when making your decision:
- Base metal
- Welding process
- Desired weld characteristics
- Budget
Choosing the Right Electrode Material for Your Welding Project:
- Consider the type of base metal you will be welding.
- The welding process used impacts electrode selection.
- Desired weld characteristics and budget should also be considered.
- Common electrode materials include carbon steel, stainless steel, aluminum, and cast iron.
Welding Electrode Maintenance Tips
Maintaining your welding electrodes is critical to ensuring the success of your welding projects.
Poorly maintained electrodes can lead to weaker welds, increased spatter, and other issues that can compromise the quality of your work.
Here are some welding electrode maintenance tips to help you keep your electrodes in top condition:
Welding Electrode Maintenance Tips:
- Store electrodes in a dry, cool place and use airtight containers or plastic bags.
- Clean electrodes before use with a wire brush.
- Regularly inspect electrodes for damage or defects and replace them as needed.
- Check the storage life and recommended amperage for electrodes.
- Replace worn or damaged electrodes for consistent, high-quality welds.
Conclusion: Maximizing Your Welding Potential with the Right Electrode Material
In conclusion, choosing a suitable electrode material is crucial to maximizing your welding potential.
Each electrode material has pros and cons that should be carefully considered based on your specific welding application. Proper electrode maintenance is also essential for producing high-quality welds.
By understanding the benefits and drawbacks of different electrode materials and following best practices for electrode maintenance, you can achieve the best results for your welding projects.